Sector News > Robotics & Automation
Industry Insights: New Tariff and Trade Policies
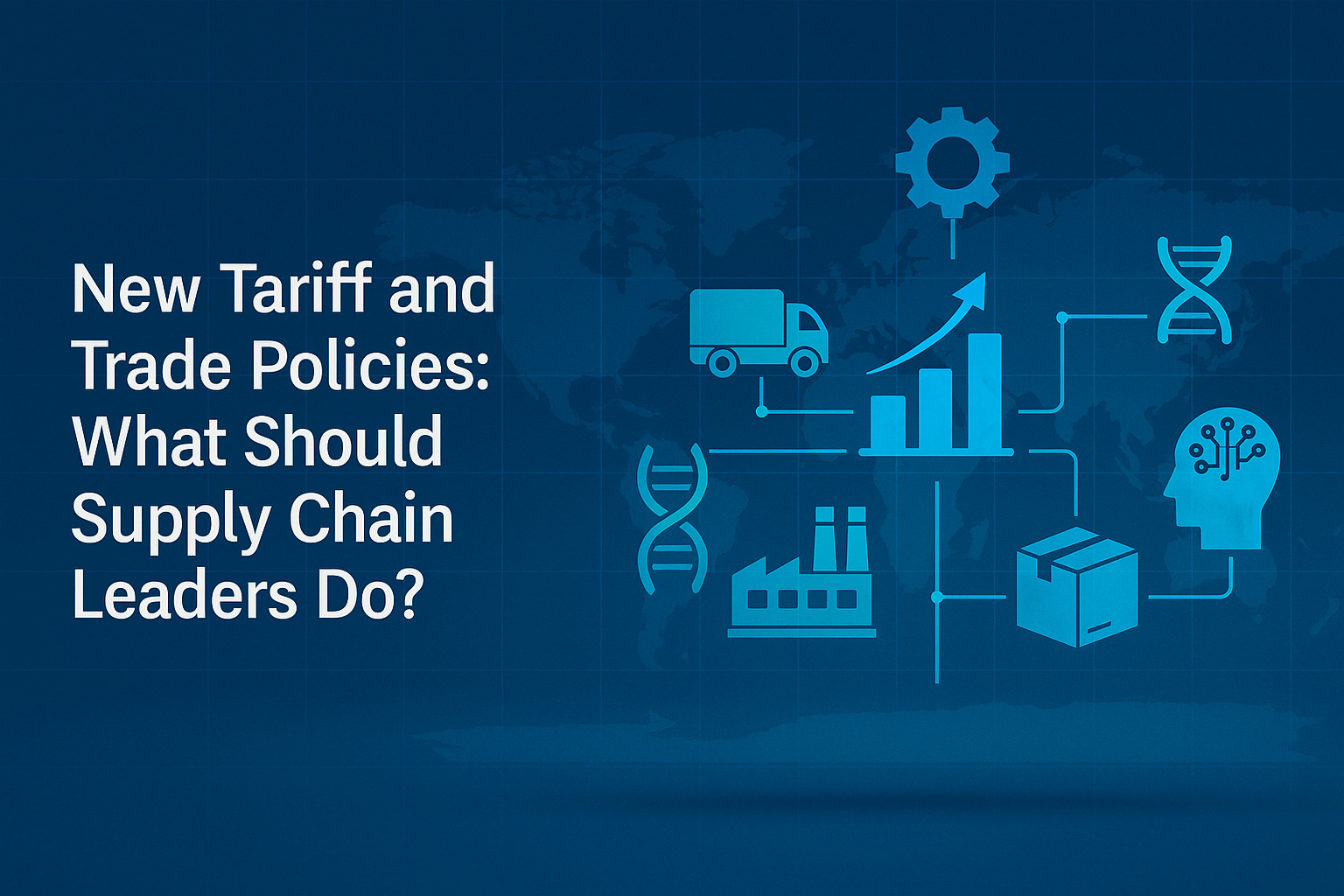
By Marie Carter-Robb • Posted in Robotics & Automation
By Adrian Wood, Director of Strategic Business Development at DELMIA
The need to react to unexpected global disruption is now a fundamental requirement for all companies - tariffs are only the latest incarnation of what manufacturers have to deal with.
Personally and professionally, the impact of recent US government policy around trade and tariffs is felt by all of us. From a business perspective, tariffs represent a major concern for companies looking at corporate goals and metrics in both the short and long-term. It has now become unclear exactly what the cost of doing business will be, and how consumer demand may shift, based upon personal preferences and spending ability.
However, this is not really uncharted territory. Over the last decade, the world has faced many disruptive events: Brexit, COVID, the Suez Canal crisis, geopolitical conflicts, climate changes, and so on. Each one is unique, but they all cause similar impacts on supply chains and manufacturing - breaks in global supply, extreme fluctuations in demand, and unknown costs and barriers to competing.
Tariffs and Twins – The Critical Connection Between Disruption, AI and Virtual Twins
In each case, business leaders in supply chain and manufacturing are faced with the same basic questions:
-
What is the impact of the disruption?
-
What should I do now?
-
What can I do to be better prepared in the future?
Prior to the globalisation of trade and the increase in product and supply chain complexity, the first two questions were difficult but not impossible to solve. The third question was often ignored or de-prioritised. Today - with COVID being the pivot point in my opinion - all three questions have become both critical and impossible to answer without the help of technology.
This is where Virtual Twins and AI capabilities have become essential in helping companies to be agile and resilient to disruption. Let us look at how they help with each of these fundamental questions:
What is the impact of the disruption?
This was the biggest - certainly the first - question from companies at the start of COVID, leading to much analysis and investment in the “control tower” concept. Yet a control tower is only part of the solution. What people were actually asking for was a precise digital representation of the entire supply chain, with end-to-end and top-to-bottom detail and real-time operational status of facilities, resources and products - also known as the Virtual Twin.
With tariffs, the Virtual Twin acts as a source of truth that enables companies to see the current state of production and fulfilment, the source of all materials, and the processes by which inventory and products move across borders before reaching customers. It allows companies to immediately identify vulnerable points of supply, new costs, and opportunities to leverage existing contingencies based upon real-time availability and capabilities.
What should I do now?
Even with a precision Virtual Twin, the complexity of global supply chains and the number of possible business permutations are beyond human comprehension to evaluate effectively. However, traditional AI methods, such as optimisation, are now adept at considering competing business priorities to balance supply and demand, while factoring in physical and logical constraints.
Used alongside the Virtual Twin model, manufacturing and supply chain leaders can experience unlimited what-if scenarios to determine tactical responses.
Tariffs may not represent a physical constraint, but cost is a major driver in optimising supply chains and production plans. Experimentation enables companies to explore questions such as: at what tariff percentage might we absorb costs to protect margins without having to pass them onto the consumer and impact demand? These are logical but extraordinarily difficult questions to answer without technology.
What can I do to be better prepared in the future?
One of the stated goals of recent policy is to bring manufacturing back to the United States, essentially onshoring production that previously developed in economically advantageous regions. Without debating the policy, the key strategic questions to mitigate the impact of tariffs on production locations are:
-
What is the increase in operational costs based on the movement of inventory and products?
-
What would the reduction in operational costs be assuming similar production capabilities in the US?
-
What is the capital investment required to expand or build new manufacturing capacity?
The Virtual Twin of the supply chain helps answer the first two questions by applying AI to models of the existing enterprise and a variety of rapidly created what-if scenarios. Question three requires a Virtual Twin model of production systems, to accurately evaluate new or adapted facilities and manufacturing processes. These twin models must work in orchestration to ensure confidence in what are likely to be billion-dollar decisions.
The precision of the Virtual Twins is critical because so many factors must be considered. For example, it is unclear whether there will be enough skilled workers to support a resurgence in manufacturing, meaning robotics and automation must also be incorporated into the future manufacturing process. The smallest of details can have a major impact on the final result.
There are also short- and medium-term strategies that can help. One option is to redesign products to reduce reliance on supply and parts requiring multiple border crossings - another valuable application of Virtual Twin technology and what-if simulation.
Of course, the best course of action to prepare for the future is to consider Virtual Twin technology today, if you have not already done so. Ironically, today’s uncertainty may itself be the greatest barrier to investment in digital transformation, as companies freeze budgets while awaiting greater clarity. However, the next disruption is always just around the corner, and from another unexpected direction. There is rarely a “best time” to act, but there is never a wrong time to make a start.