Future-Facing Facades: ACS Stainless on Safety, Skills and Sustainability
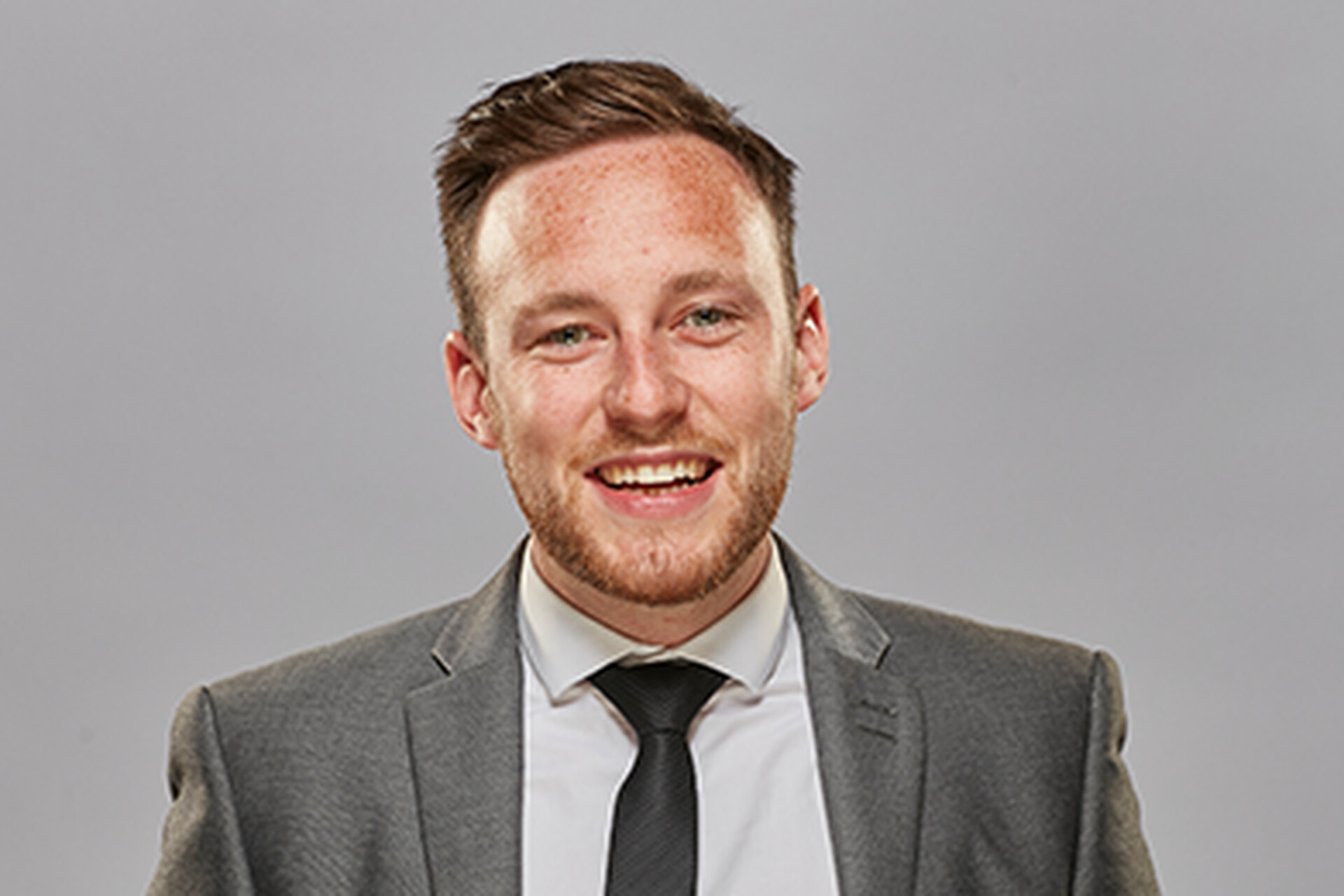
By Marie Carter-Robb • Posted in Engineering
Paul Ruding is Strategic Specification Director at Leeds-based ACS Stainless Steel Fixings – a leading innovator in masonry façade solutions, going beyond manufacturing to shape the future of construction. With 40 years’ experience, ACS partners with contractors and architects early in the design process, offering bespoke, sustainable solutions. Their expertise, cutting-edge technology, and commitment to safety and compliance ensures exceptional quality and efficiency.
Paul Ruding is Strategic Specification Director at Leeds-based ACS Stainless Steel Fixings – a leading innovator in masonry façade solutions, going beyond manufacturing to shape the future of construction.
With 40 years’ experience, ACS partners with contractors and architects early in the design process, offering bespoke, sustainable solutions. Their expertise, cutting-edge technology, and commitment to safety and compliance ensures exceptional quality and efficiency.
Industry Trends and Challenges
What are the biggest trends shaping engineering and manufacturing today?
“There are two major trends for me,” says Paul Ruding. “First, the skills shortage and upskilling. Our sector faces a major skills gap, making it essential to attract new talent and upskill existing workers. As the industry embraces new technologies, investment in people is vital to ensure the workforce can adopt and pioneer sustainable, efficient processes.”
The second key trend is around safety and early-stage collaboration. “The Building Safety Act has driven a stronger focus on safety, transforming manufacturers like ACS into early-stage design partners. Collaborating with contractors and designers from the outset ensures products are specified early, making buildings safer and more sustainable.”
What challenges is ACS currently facing – and how are you responding?
“The biggest challenge we’re facing right now is the skills gap. Fortunately, we’re heavily investing in our colleagues’ training and development to address this.
“But it’s not just about internal growth,” Paul adds. “We’re spreading the word across the industry – I run a free CPD programme for architects and industry peers, sharing knowledge and promoting best practices across the sector. By expanding expertise beyond our own business, we aim to strengthen the industry as a whole.”
Innovation and Technology
How is ACS adopting new technologies to stay competitive – and what impact are they having?
“We’re big on investing in new technology and processes,” Paul explains. “We’ve found it saves time and cost, but also helps us operate more sustainably.”
Key examples include:
-
Digital transformation – “In the past two years we’ve made significant investments in automation, robotics and IT systems, introducing new machinery and ways of working.”
-
BIM and 3D design – “We’ve appointed two in-house software developers and a software engineer, driving forward our use of BIM and Revit. This has already delivered significant benefits to our manufacturing processes – improving efficiency, enhancing product accuracy, and ultimately providing even greater peace of mind for our customers.”
-
Futureproofing our workforce – “Through training programmes and partnerships with local education institutions, we’re equipping our team to adapt traditional manufacturing skills to automated processes.”
-
Factory expansion – “Last year we expanded our state-of-the-art manufacturing factory in Leeds with a seven-figure investment, adding 10,000 sq ft of space and robotics. It’s helped us create more innovative products, supporting contractors, developers and architects in building safer, more sustainable structures.”
Sustainability and Environmental Impact
What is ACS doing to reduce environmental impact and improve sustainability?
“We’ve recently achieved Planet Mark accreditation, becoming the first in our sector to do so,” Paul notes.
“The certification reflects ACS’s focus on measurable carbon reductions rather than offsetting alone. We’re also investing in apprenticeships, T-Levels, and workforce training, while collaborating with steel suppliers to adopt low-carbon innovations, ensuring our supply chain evolves alongside sustainable industry advancements.”
How will sustainability shape the future of manufacturing?
“Sustainability is becoming a driving force, pushing companies towards genuine carbon reductions over offsetting. The focus will be on decarbonising operations and supply chains, adopting low-carbon materials and circular manufacturing. Workforce development will also be key, with training in greener technologies ensuring industry resilience.”
“At ACS, sustainability is central to everything we do. For example, a recent independent recycling report confirmed that 98% of our waste is recycled and 0% sent to landfill – that reflects our serious commitment to minimising environmental impact.”
Workforce Development and Skills
What skills are most critical for the future workforce in this sector?
“The future workforce will need a blend of technical skills and adaptability,” says Paul. “As the manufacturing sector shifts towards robotics and advanced systems, ongoing investment in upskilling existing employees is essential to ensure they can effectively use new technologies.
“While apprenticeships and new talent remain vital, it’s equally important to empower the current workforce with the skills needed to thrive in an increasingly automated and digitally driven industry.”
How is ACS investing in training and workforce development?
“Over the past three years, we’ve welcomed new apprentices to ensure a pipeline of fresh talent. We’re also investing significantly in the training of current employees across all departments, with many colleagues actively participating in development programmes.
“Personally, I’m also furthering my education with a part-time master’s degree,” Paul adds. “And of course, there are our free CPD courses, via which we share our expertise and help the wider industry adopt best practices for creating safe, sustainable buildings. The CPDs can be hosted by me, my expert colleagues or peers in the industry, giving attendees real insight and knowledge.”
Leadership and Business Strategy
How do you maintain a culture of innovation and continuous improvement at ACS?
“We’re really innovative – and it’s largely embedded into our culture through ongoing investment in technology, training and collaboration.
“We actively embrace digital transformation, incorporating robotics, automation and advanced IT systems to enhance efficiency and precision. Our partnerships with educational institutions help us nurture talent and foster fresh thinking, while internal initiatives like the ACS Academy ensure continuous upskilling of our workforce. This focus on learning and adaptability keeps us ahead of industry trends.”
What’s your vision for the future of the company – and how will you achieve it?
“As our MD recently wrote, ACS aims to lead the industry in sustainable, technology-driven manufacturing.
“Our vision includes continued expansion, with significant investments in facilities, automation, and low-carbon materials. We’re committed to pioneering safer, more sustainable construction solutions by working closely with clients from the design stage to optimise efficiency and compliance.
“By prioritising sustainability, innovation, and workforce development, ACS plans to remain at the forefront of manufacturing excellence.”